Quality Control in CNC Machining: Best Practices and Strategies
Quality Control in CNC Machining: Best Practices and Strategies
In today's manufacturing landscape, Computer Numerical Control (CNC) machining plays a pivotal role in producing high-precision components for industries such as aerospace, automotive, medical, and electronics. As demand for tighter tolerances and consistent quality increases, ensuring quality control in CNC machining has never been more critical.
This article explores key quality control strategies in CNC machining, their importance, tools and technologies involved, and best practices manufacturers can implement to maintain high-quality standards in their operations.
What Is CNC Machining Quality Control?
CNC machining quality control refers to the processes and systems in place to ensure that machined parts meet predefined specifications and tolerances. It encompasses every stage of production—from design and programming to machining, inspection, and post-processing.
The main goal of quality control in CNC machining is to minimize defects, reduce rework, improve efficiency, and deliver parts that conform to customer expectations and industry standards.
Why Quality Control Is Crucial in CNC Machining
Precision is the hallmark of CNC machining. However, without stringent quality control, even the most sophisticated CNC machines can produce inconsistent or flawed parts. Here's why quality control is essential:
-
Customer Satisfaction: High-quality parts meet client expectations, fostering trust and long-term business relationships.
-
Cost Reduction: Detecting defects early reduces waste, rework, and the associated costs.
-
Compliance: Many industries require strict adherence to international standards such as ISO 9001, AS9100, or IATF 16949.
-
Operational Efficiency: A well-structured QC process improves workflow and ensures timely delivery.
Core Elements of CNC Quality Control
To achieve consistent quality, manufacturers must adopt a holistic approach that addresses the following components:
1. Design Validation
Before machining begins, the CAD (Computer-Aided Design) model must be reviewed for feasibility. Engineers verify dimensions, tolerances, and material specifications to ensure they are compatible with machining capabilities.
2. CAM Programming Review
CAM (Computer-Aided Manufacturing) software converts the CAD model into machine-readable G-code. Any error at this stage can affect the final output. An internal review of the toolpaths, feed rates, and cutting strategies is essential.
3. Tool and Machine Calibration
Regular calibration of CNC machines, cutting tools, and inspection equipment ensures precision. Misalignment, tool wear, or temperature drift can result in dimensional deviations.
4. In-Process Inspection
In-process inspection involves checking dimensions during the machining process to catch errors early. Techniques include:
-
Touch probe measurements
-
Laser scanning
-
Manual calipers and micrometers
These inspections help prevent cumulative errors and reduce waste.
5. Final Part Inspection
Once machining is complete, a thorough inspection is conducted using advanced metrology tools:
-
Coordinate Measuring Machine (CMM): Measures complex geometries with high accuracy.
-
Optical Comparators: Project a magnified image to compare the part with design standards.
-
Surface Roughness Testers: Evaluate the texture and finish of the machined surface.
6. Documentation and Traceability
Quality control is not just about inspection—it's about recordkeeping. Detailed documentation helps trace issues back to their root cause and supports audits or customer evaluations.
Quality Control Tools and Technologies
Modern CNC shops employ a variety of tools to maintain consistent quality. Some of the most commonly used technologies include:
-
Statistical Process Control (SPC): Monitors process stability using statistical methods.
-
Digital Twin Technology: Simulates the machining process digitally to predict and correct issues before production.
-
Machine Monitoring Software: Tracks tool wear, vibration, and machine conditions in real-time.
-
Automated Inspection Systems: Robots and vision systems perform high-speed quality checks without human intervention.
Common Quality Issues in CNC Machining—and How to Prevent Them
Despite advanced equipment, quality issues can still arise. Here are some of the most common problems and how to mitigate them:
1. Dimensional Inaccuracy
-
Cause: Tool wear, thermal expansion, incorrect toolpaths
-
Solution: Regular tool changes, temperature compensation, simulation verification
2. Surface Imperfections
-
Cause: Inadequate feeds and speeds, dull tools
-
Solution: Optimize cutting parameters and implement tool maintenance schedules
3. Burrs and Sharp Edges
-
Cause: Improper tool selection or cutting direction
-
Solution: Use deburring tools or secondary finishing operations
4. Material Deformation
-
Cause: Incorrect clamping, excessive heat
-
Solution: Use soft jaws or custom fixtures, apply coolant
Best Practices for CNC Quality Control
Implementing a robust quality control system requires a strategic approach. Here are several best practices manufacturers can adopt:
1. Standardize Procedures
Establishing standard operating procedures (SOPs) ensures consistency in how parts are programmed, machined, and inspected. SOPs also make it easier to train new operators and scale operations.
2. Invest in Employee Training
Even with automation, human expertise remains vital. Skilled machinists and quality engineers are essential for interpreting data, maintaining equipment, and making real-time decisions.
3. Use Preventive Maintenance
Regular maintenance of machines and tools prevents unexpected downtime and ensures they operate within tolerance.
4. Embrace Automation
From CAM software to automated inspection systems, embracing technology increases efficiency and minimizes human error.
5. Feedback Loops
Implement closed-loop feedback systems that use inspection data to make adjustments in real-time. This proactive approach enhances accuracy and productivity.
Quality Standards and Certifications
To demonstrate their commitment to quality, many CNC machining shops pursue industry certifications such as:
-
ISO 9001: General quality management system
-
AS9100: Aerospace industry requirements
-
IATF 16949: Automotive industry standards
-
ISO 13485: Medical devices
Achieving these certifications involves rigorous audits, documentation, and continual improvement.
The Role of Continuous Improvement
Quality control isn't a one-time process—it's a mindset. Lean manufacturing, Six Sigma, and Kaizen are all methodologies that support continuous improvement in CNC machining.
By analyzing root causes, reducing variability, and streamlining workflows, companies can continually raise the bar for quality.
Conclusion
In the high-stakes world of precision manufacturing, CNC machining quality control is more than just a final inspection—it's a comprehensive strategy that touches every phase of production. Through a combination of skilled personnel, modern technology, and structured processes, manufacturers can ensure that each component meets the highest standards.
Implementing a robust quality control framework not only boosts product reliability but also enhances brand reputation, reduces operational costs, and fosters long-term customer loyalty. In a competitive market, consistent quality is not just an advantage—it's a necessity.
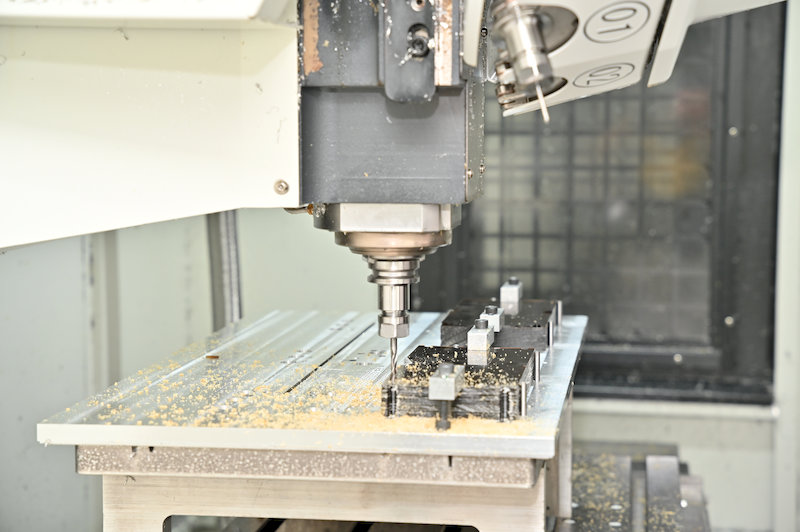